Executive Summary
A major automotive parts manufacturer faced high steam costs and inefficiencies with a 1.5 TPH steam boiler consuming 665 KL of diesel annually. High fuel costs and also issues of fuel pilferage were a major concern for management. Energeia converted the boiler to run on natural gas, upgraded the control system, and added IoT monitoring, resulting in 40% fuel cost savings and reduced emissions.
Key Stats
Fuel Cost Savings
Diesel Saved Annually
CO₂ Emission Reduction
Customer Overview
The factory is a major manufacturer of automotive parts, specializing in exhaust systems and related components for two-wheelers and four-wheelers. As a key supplier to renowned global brands such as Honda, Suzuki, Yamaha, Daikin, and Paramount, the company’s parent has 10+ facilities across the world.
The Challenges
The company was facing several challenges that were significantly impacting their operational costs:
- High Boiler Operating Costs: The cost of running their steam boiler was exceedingly high.
- Rising Diesel Prices: Increasing diesel prices further exacerbated the financial burden.
- Lack of Energy Consumption Visibility: The company was unable to accurately measure the energy consumption of their boiler, making it difficult to identify opportunities for cost savings.
The company’s 1.5 TPH steam boiler, which was essential for running operations, originally consumed 95 liters of diesel per hour. Given that the plant operated for 7,000 hours annually, this translated to a consumption of 665 KL of diesel each year.
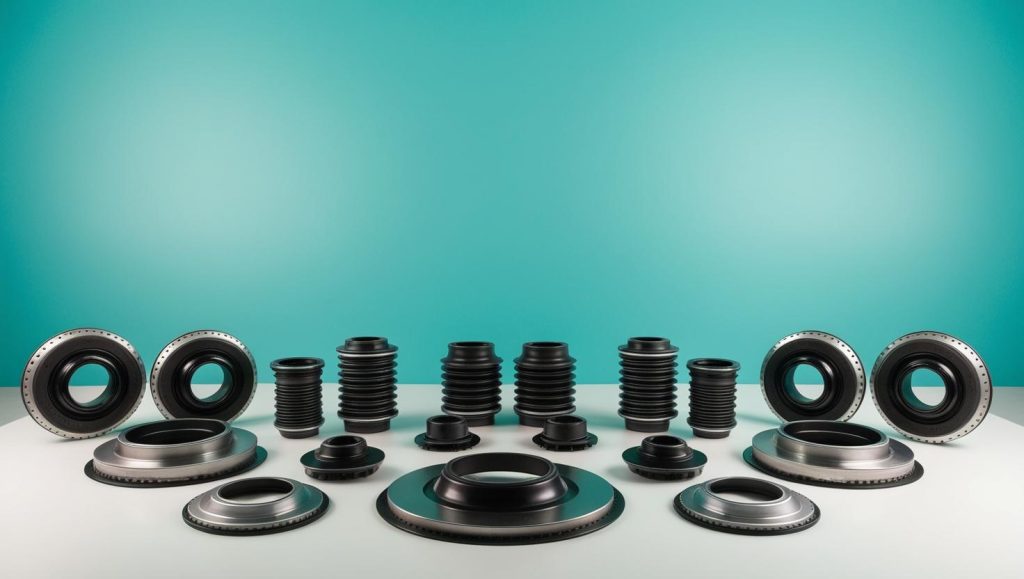
Energeia’s Solution: Boiler Fuel Conversion Project
Energeia proposed a comprehensive solution to address the company’s challenges. The project involved several key components:
Boiler Fuel Conversion Implementation
- End-to-End Project Management: Energeia managed the entire project, from initial planning to execution, ensuring seamless integration with the company’s existing systems.
- Internal Pipeline Modification: The internal pipeline was modified to accommodate the new fuel type.
- Boiler Conversion: The existing boiler was converted from diesel to natural gas, including the installation of a new burner.
- Control System Upgrade: The boiler’s control system was upgraded to enhance efficiency and reliability.
- IoT Monitoring System: Energeia implemented an IoT monitoring system to provide real-time data on energy consumption, enabling better management and optimization.