Executive Summary
A Tier 1 automobile component manufacturer in North India sought to optimize energy consumption at its air compressor plant. With four air compressors and a total capacity of 1,700 CFM, the facility faced significant energy consumption issues, averaging 2,500-2,800 kWh per day. Energeia implemented advanced monitoring and control solutions, which identified significant energy and cost savings.
Key Stats
Monetary Savings Annually
Energy Savings Annually
CO₂ Emission Reduction
Customer Overview
The facility is a Tier 1 automotive component manufacturer in North India, operating with a robust air compressor system integral to its manufacturing processes.
- Average Air Demand: 700 CFM
- Average Daily Energy Consumption: 2,500-2,800 kWh
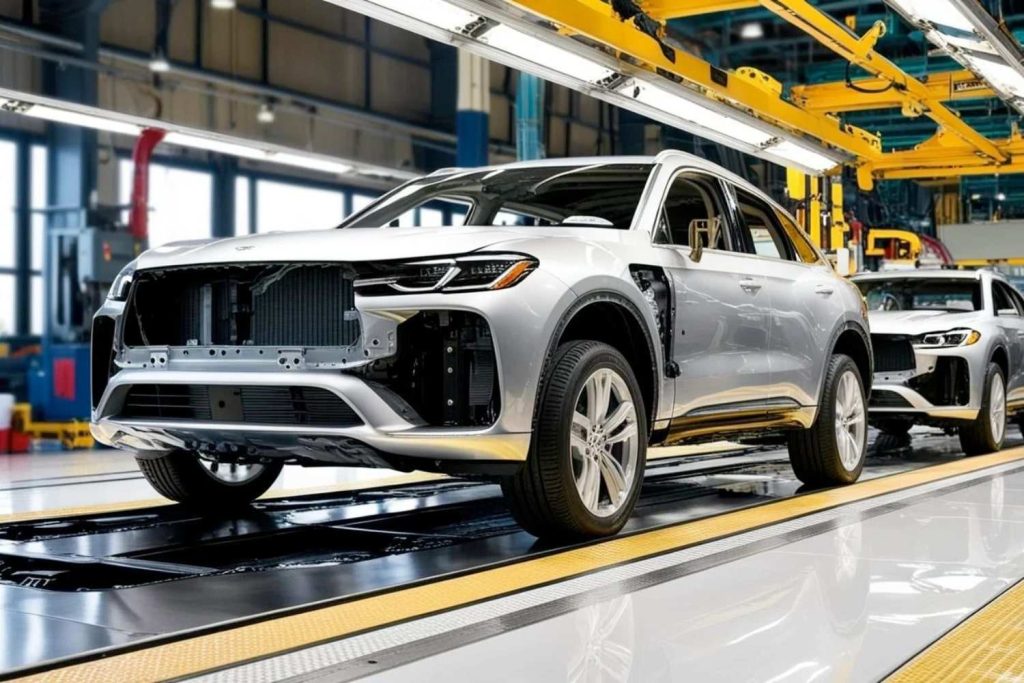
The Challenges
The facility faced several challenges:
- High Energy Consumption: The plant’s air compressors consumed a large amount of electricity, varying based on daily and weekly demand fluctuations.
- Pressure Drop Issues: A critical pressure drop in one production area affected efficiency and energy consumption.
- Inconsistent Load Management: The plant struggled with maintaining optimal compressor operation throughout the day.
Energeia’s Solution: E-Air Optimization
Energeia deployed its IoT-based monitoring system to find inefficiencies and implemented Energy Conservation Measures, which cost 0 CAPEX featuring:
- Sensors & Data Acquisition: Energy meters, pressure sensors, and flow meters were installed to capture data at one-second intervals over 30 days.
- Advanced Analytics: Analysts used the monitoring data to identify energy-saving measures and diagnose causes of pressure drops.
- Identification of Inefficient Air Compressors: As the the plant had 4 Air Compressors, out of which 2 were being used at one time, through continuous monitoring, the most efficient combination of Air Compressors were identified
- Pressure-Based Control System: A pressure-based control system was introduced to ensure the most efficient combination of compressors operated based on plant demand.
- Load/Unload Pressure Settings: Adjustments were made to specific compressors, reducing pressure drops and further increasing energy savings.
ESCO Shared Savings Model
In Energeia’s Shared Savings Model, Energeia funded and implemented energy efficiency improvements for the client. The client paid nothing upfront, as Energeia covered all costs, including equipment, installation, and maintenance. Once the project began saving energy, the cost savings were split between Energeia and the client.