When it comes to industrial equipment, many businesses focus on purchase price as the primary factor in decision-making.
But what if we told you that the sticker price is just the tip of the iceberg?
The real cost of owning and operating machinery—whether it’s an air compressor or chiller —goes far beyond the initial investment.
This is where Total Cost of Ownership (TCO) for Industrial Equipment comes into play.
TCO accounts for every expense tied to a machine’s lifecycle, from energy consumption and maintenance to downtime and eventual disposal.
Understanding TCO prevents costly surprises and helps businesses make smart, long-term investments.
In this post, we’ll break down the TCO of two critical industrial systems—air compressors, and and chillers—to help you uncover hidden costs and optimize your bottom line.
But first, let’s quickly look at a real-world story that highlights the importance of keeping TCO in mind while procuring any heavy machinery for a factory.
The Story of a Costly Miscalculation in a Factory
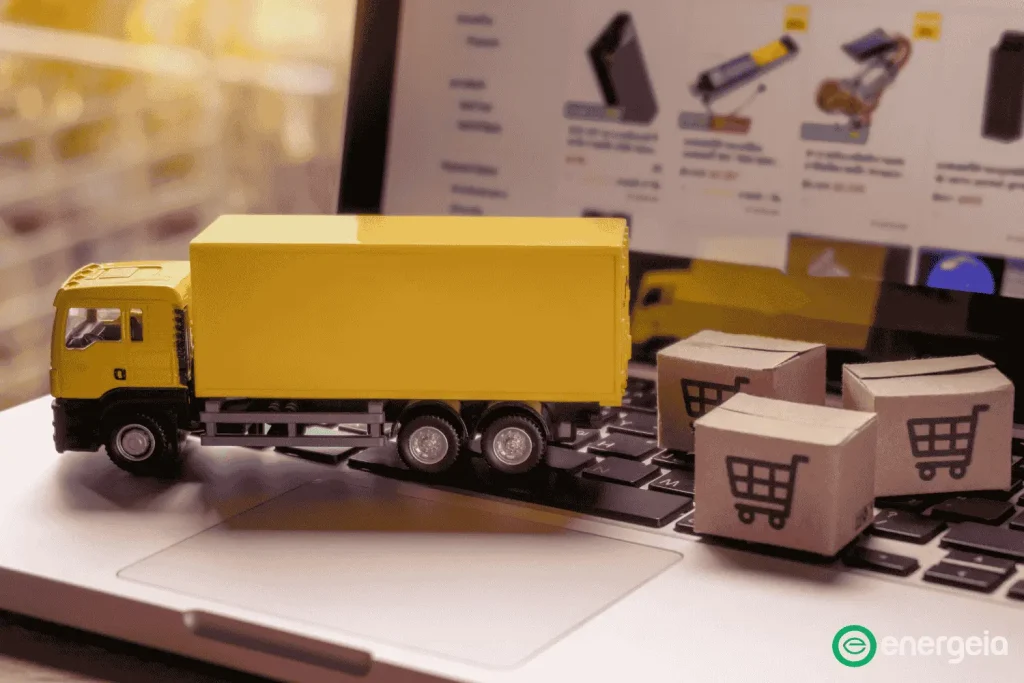
Ramesh, the operations manager of a mid-sized textile factory in Gujarat, was under pressure. His company needed to upgrade its air compressors before peak production season. With tight budgets, he chose the cheapest model available in the market, convinced that he was making a financially sound decision.
For a while, things seemed fine. But within a few months, the electricity bills shot up. Workers started complaining about pressure drops, which slowed production. Routine maintenance turned into costly emergency repairs, and worst of all, downtime losses exceeded ₹10 lakh in just a year.
Ramesh had fallen into a common trap: focusing on upfront cost instead of TCO. If he had invested in a higher-efficiency air compressor, he could have saved on energy costs, reduced breakdowns, and ensured smooth operations—ultimately saving the company money in the long run.
His story isn’t unique. Many Indian industries—whether in textiles, pharmaceuticals, food processing, or heavy manufacturing—face similar challenges.
Let’s break down how TCO impacts air compressors and chillers, and how businesses can make smarter investment decisions.
TCO for Industrial Air Compressors
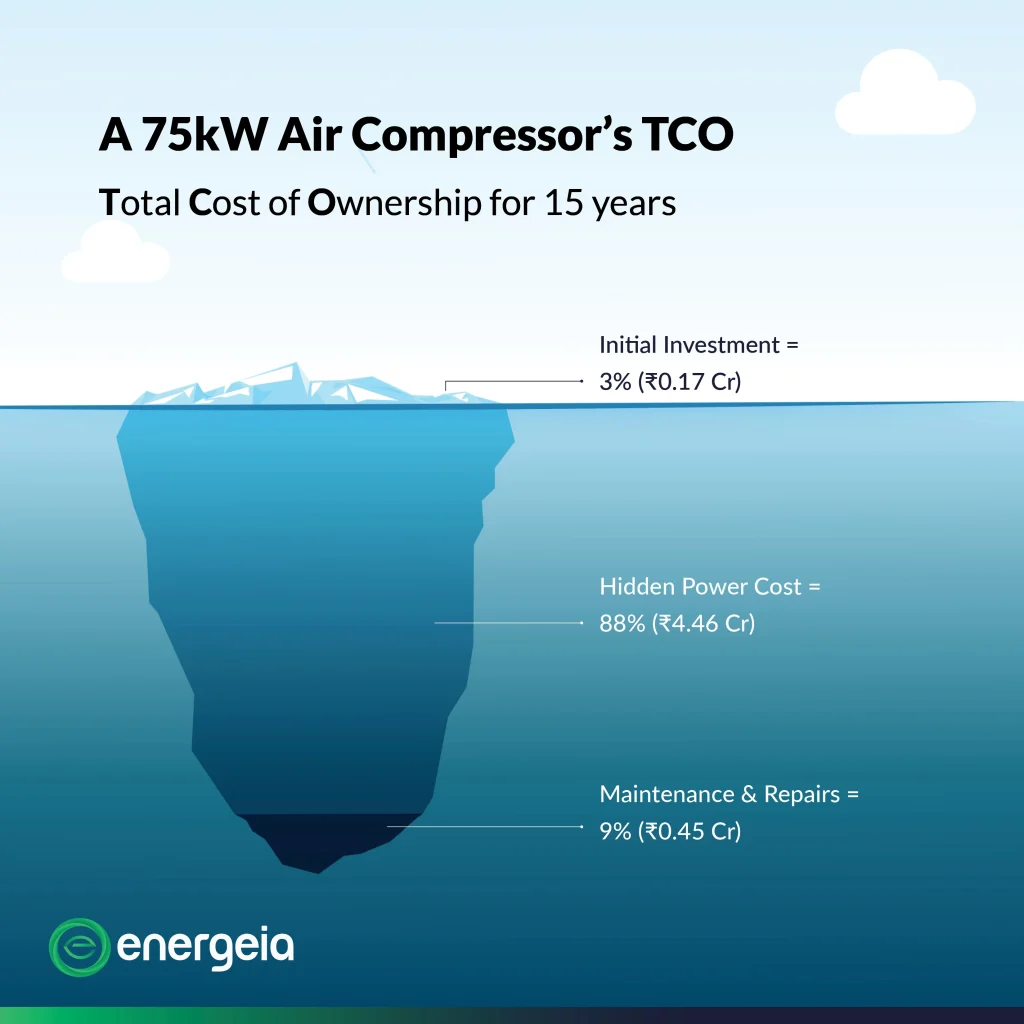
Air Compressors: Total Cost Insights
Type of Cost | Description | Typical Contribution to TCO |
Initial Investment | Compressor purchase, installation, piping, electrical setup | 2-10% |
Hidden Power Cost | Power usage (kWh/year), efficiency rating (CFM/kW) | 65-90% |
Maintenance & Repairs | Routine servicing, parts replacement, moisture removal, filtration | 5-10% |
- Energy costs dominate – 65-90% of total ownership costs come from electricity consumption.
- Compressed air leaks = wasted money – Up to 30% of generated air is lost through leaks.
- Predictive maintenance reduces costs – IoT-based monitoring can cut downtime and repair expenses by 25%.
Key Savings Strategies for Air Compressors
✅ Invest in high-efficiency compressors (CFM/kW optimized)
✅ Regularly check for air leaks to reduce waste
✅ Lower system pressure by just 10 PSI to cut energy costs by 7%
Real-world Example
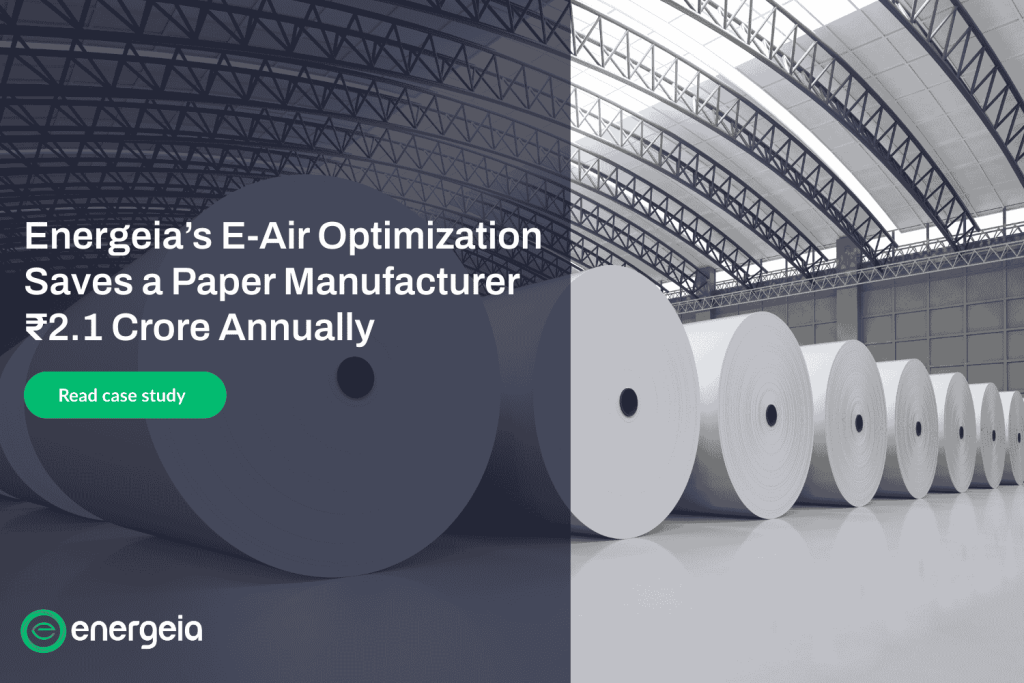
Unsure of how to fund such CAPEX-heavy compressor upgrades?
We understand that it’s difficult to allocate a large budget for such expensive upgrades. That’s why Energeia offers multiple flexible financing models to make sure you can reduce your energy and equipment costs without straining your cashflow.
Read about how our unique pay-as-you-save model enabled a Metal Manufacturer in NCR to cut annual energy costs by 37% with zero upfront investment.
TCO for Industrial Chillers
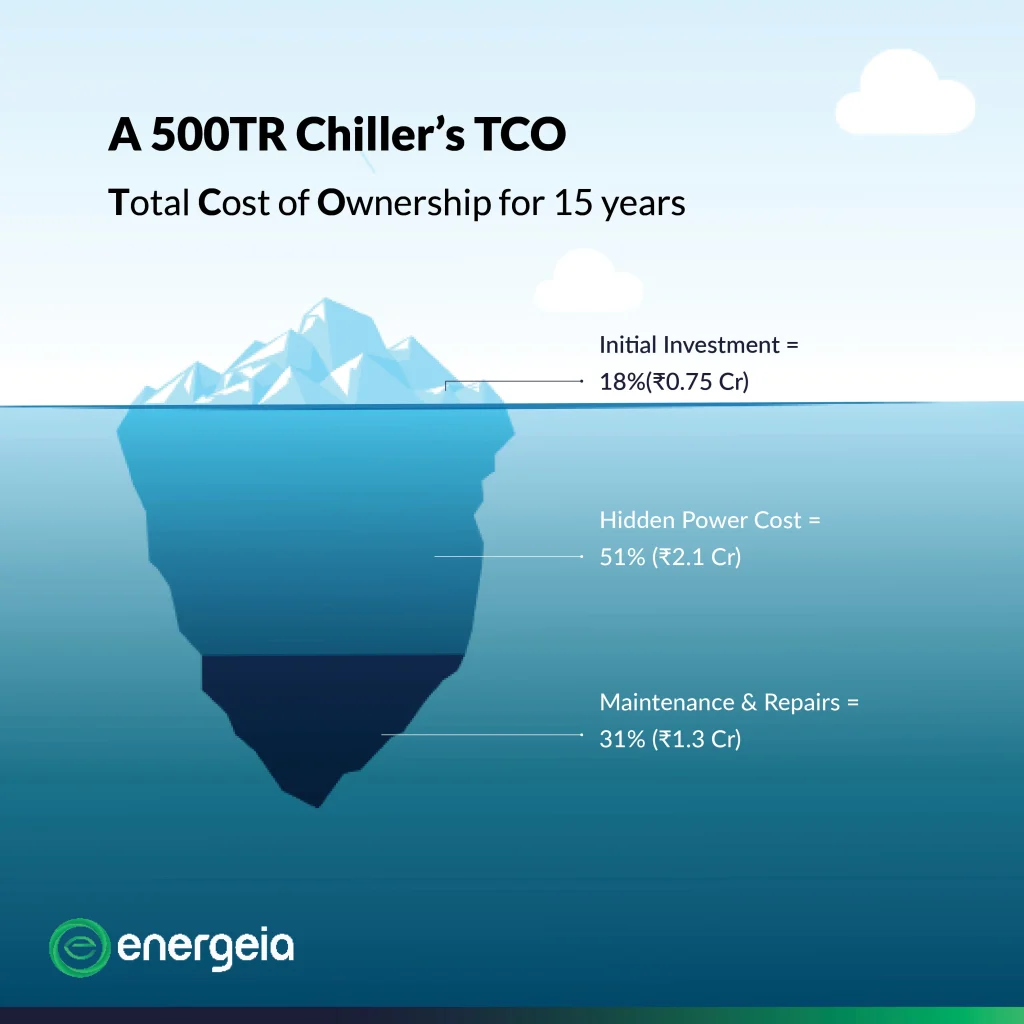
Chillers: Total Cost Insights
Type of Cost | Description | Typical Contribution to TCO |
Initial Investment | Chiller purchase, installation, piping, electrical setup | 2-20% |
Hidden Power Cost | Power usage (kWh/year), efficiency (COP/EER) | 50-70% |
Maintenance & Repairs | Servicing, parts replacement (fans, coils, pumps, filters), water and chemical use | 25-35% |
- Energy is the biggest expense – 50-70% of TCO comes from invisible power consumption.
- Water-cooled vs. air-cooled? – Water-cooled chillers are more efficient but have higher maintenance & water treatment costs.
- Downtime is expensive – Predictive analytics reduces failures by 20%, preventing costly production halts.
Key Savings Strategies for Industrial Chillers
✅ Choose high COP/EER chillers to improve efficiency
✅ Implement demand-based cooling controls to optimize power use
✅ Regularly maintain cooling towers and water treatment systems
Real-world Example
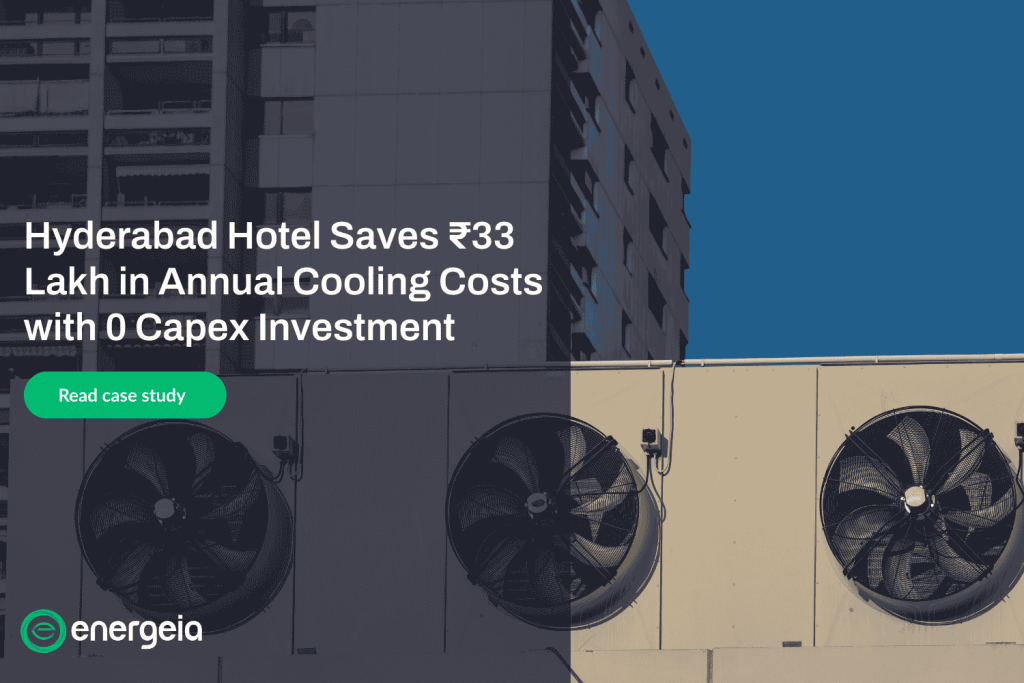
Final Thoughts
Invest Smart, Save Big
The true cost of industrial equipment extends far beyond the initial purchase price. As seen with air compressors and chillers, energy consumption, maintenance, and downtime can add up to crores in hidden expenses over the equipment’s lifecycle.
Businesses that focus solely on upfront costs often find themselves trapped in a cycle of higher energy bills, frequent repairs, and lost productivity—leading to substantial financial losses.
However, companies that take a Total Cost of Ownership (TCO) approach can unlock significant long-term savings. Investing in high-efficiency systems, predictive maintenance, and smart energy monitoring not only reduces operational costs but also enhances reliability and sustainability.
Are you looking to reduce your industrial equipment’s costs? We can build a custom TCO analysis for your industrial machinery to help you maximize your cost savings and minimize your emissions.
Consult with Energeia today to take the first step toward smarter investment decisions for tomorrow.
📞 Book a Complimentary Energy Appraisal Today: +91 9319271849
✉️ Email: sales@energeia.in