Executive Summary
A leading textile exporter in Bangladesh faced issues with air compressor efficiency and energy tracking. Energeia’s E-Air solution provided audits and recommendations, leading to annual savings of 1.92 Crore BDT (Bangladeshi Taka) and improved efficiency.
Key Stats
Monetary Savings Annually
Energy Savings Annually
CO₂ Emission Reduction
Customer Overview
One of the largest textile exporters in Bangladesh operates a large air compressor plant that plays a crucial role in its manufacturing processes.
- “>Annual Air Compressor Plant Energy Consumption: 4.5 GWh
- Annual Air Compressor Energy Spend: 5.4 Crore BDT
- Average Daily Energy Consumption (All Compressors): 14 MWh – 15.5 MWh
The Challenges
The textile exporter faced several challenges with their air compressor plant, which led to increased operational costs and inefficiencies:
- Lack of Precise Monitoring: The company struggled to track the exact energy consumption of each air compressor, making it difficult to manage energy usage effectively.
- Efficiency Variations: There were noticeable variations in the efficiency of different air compressors, but the reasons were unclear.
- Pressure Drop Issues: The system experienced pressure drops across the air compressor network, impacting overall performance.
- Lack of Insights: The company lacked the necessary insights to understand why these inefficiencies were occurring.
- Rising Compressed Air Costs: The cost of compressed air was increasing in relation to production, adding to the operational burden.
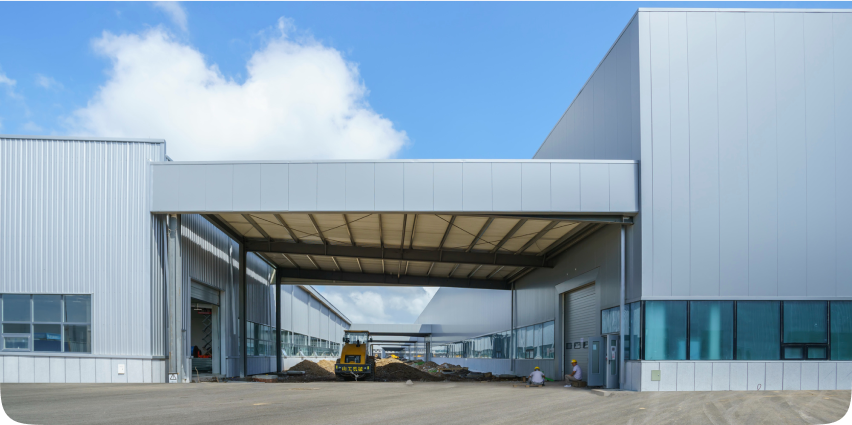
Energeia’s Solution: E-Air Optimization
Energeia implemented a tailored E-Air solution to address the challenges faced by the facility. The approach involved a comprehensive audit and monitoring service, which included the following steps:
- Continuous IoT Monitoring: Real-time energy consumption of each compressor was monitored to identify usage patterns and inefficiencies. The plant’s efficiency was evaluated by comparing energy consumption with demand flow (kW/CFM).
- Compressor Assessment: The capacity and efficiency of each compressor were measured in terms of Free Air Delivery (FAD) and kW/CFM, providing a clearer understanding of overall performance.
- Pressure Profiling: Conducted pressure profiling on both the supply and demand sides to identify discrepancies and opportunities for optimization.
- Air Leak Audit (LDAR): An air leak audit was performed to quantify losses within the system, leading to targeted repair measures.
- Air Quality Audit: Dew point monitoring was carried out at both supply and demand centers to ensure optimal air quality and system performance.
- Demand Monitoring: Air demand during daily production was tracked to better align supply with actual needs, improving efficiency.
- Pressure-Based Control System: Adjustments were made to the pressure-based control system to ensure the most efficient combination of compressors operated according to demand.
- Replacement of Inefficient Compressors: Identified and replaced four inefficient compressors, improving the average kW/CFM and unlocking significant energy savings.
- Optimized Low-Pressure Areas: Areas requiring lower pressure compressed air (4 bar) were optimized by placing low-pressure air compressors closer to consumption points, resulting in additional energy savings.