Executive Summary
An established Indian sheet metal manufacturer based in Greater Noida, UP, was experiencing inefficiencies in its compressed air system, leading to high energy costs and operational challenges. Energeia conducted a thorough audit of the company’s air compressors, providing key insights and proposing a series of improvements, including compressor replacements, pipeline upgrades, and the implementation of a new air receiver tank and dryer. Energeia financed and implemented these improvements leading to significant energy and cost savings as well as enhanced operational efficiency for the company.
Key Stats
Monetary Savings Annually
Energy Savings Annually
CO₂ Emission Reduction
Customer Overview
The company specializes in manufacturing sheet metal components and assemblies for multinational corporations such as LG Electronics, Samsung, and Honda Motorcycles & Scooters. With decades of experience, the company has grown into a key player in India’s manufacturing sector, boasting a strong reputation for quality and innovation.
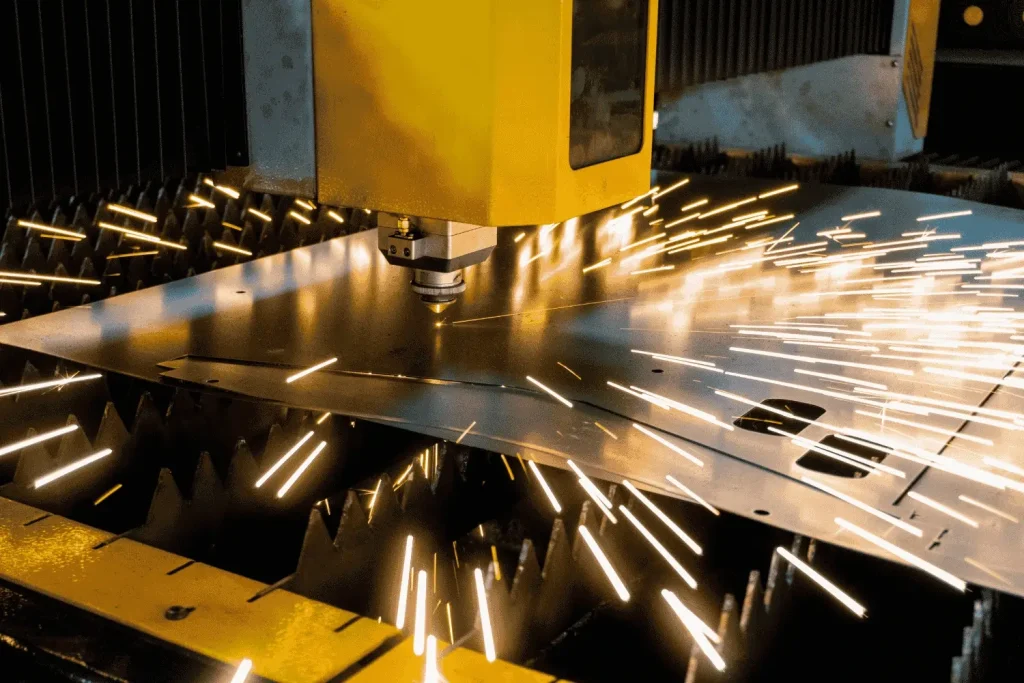
The Challenges
The manufacturer was dealing with multiple issues surrounding its compressed air system:
- Lack of Energy Tracking: There was no way to monitor the exact energy consumption of individual compressors, making it difficult to measure efficiency.
- Inefficient Air Compressors: Different compressors showed low levels of efficiency, leading to energy wastage.
- Pressure Drops: The system faced pressure drops, affecting operational performance.
- Limited Insights: The company lacked the data needed to understand the causes behind these inefficiencies, resulting in suboptimal decision-making.
Energeia’s Solution: E-Air Optimization
Energeia introduced its E-Air solution, starting with a comprehensive audit of the compressed air system. The audit provided detailed insights into energy consumption, system efficiency, and operational bottlenecks. Post audit, Energeia and the customer signed an ESCO Shared Savings Contract for a tenure of 5 years, in which Energeia would finance, install and maintain energy efficient equipment technology in the Air Compressor Plant, in return for a share of the savings. Key actions included:
- Audit of Air Compressors:
- Monitoring the current consumption of each compressor to assess individual performance.
- Measuring plant-wide efficiency by comparing energy consumption with demand flow.
- Pressure profiling to analyze pressure levels on both the supply and demand sides.
- Day-to-day air demand monitoring to identify usage patterns.
- Walk-through audit of the entire compressed air network to spot inefficiencies.
- Identifying energy conservation measures (ECMs) to optimize power consumption.
- Analyzing pressure differences within the generation side of the systems.
- Energy Conservation Measures in ESCO Agreement:
- Replacement of inefficient air compressors with VFD driven energy efficient Air Compressors
- Construction of a new compressor room to centralize operations.
- Installation of a modern compressed air pipeline to reduce pressure drops and improve flow.
- Addition of an air receiver tank with a level-based drain system for better air storage and distribution.
- Replacement of the existing desiccant dryer with a no loss air dryer
- Leak repairs throughout the system to prevent air loss and reduce energy consumption.
ESCO Shared Savings Model
In Energeia’s Shared Savings Model, Energeia funded and implemented energy efficiency improvements for the client. The client paid nothing upfront, as Energeia covered all costs, including equipment, installation, and maintenance. Once the project began saving energy, the cost savings were split between Energeia and the client.