Executive Summary
A yarn dyeing export company in Bangladesh faced high energy costs due to aging pumps and no energy monitoring system. Energeia’s audit identified inefficiencies leading to the replacement of old pumps with efficient IE-3 motors, leading to annual savings of 20,12,000 kWh and 2.4 Crore BDT (Bangladeshi Taka).
Key Stats
Monetary Savings Annually
Energy Savings Annually
CO₂ Emission Reduction
Customer Overview
A leading yarn dyeing company based in Bangladesh produces dyed cotton, synthetic, and cotton-synthetic blended yarn as well as sewing and embroidery thread for the export-oriented readymade garment (RMG) industry. It has an annual production capacity of 4,200 MT.
The Challenges
The company struggled with several challenges related to their pump systems:
- Aging Pump Infrastructure: The existing pumps were old and consumed more energy than necessary.
- Incorrectly Sized Equipment: Most of the pumps were sized incorrectly, leading them to run on inefficient operating points
- Lack of Efficiency Monitoring: There was no method in place to identify the efficiency of individual pumps.
- Invisible Energy Costs: The company had no visibility into the energy costs associated with each pump.
- High Operational Costs: Due to unknown pump efficiencies and the lack of digital continuous monitoring, the company faced escalating energy costs.
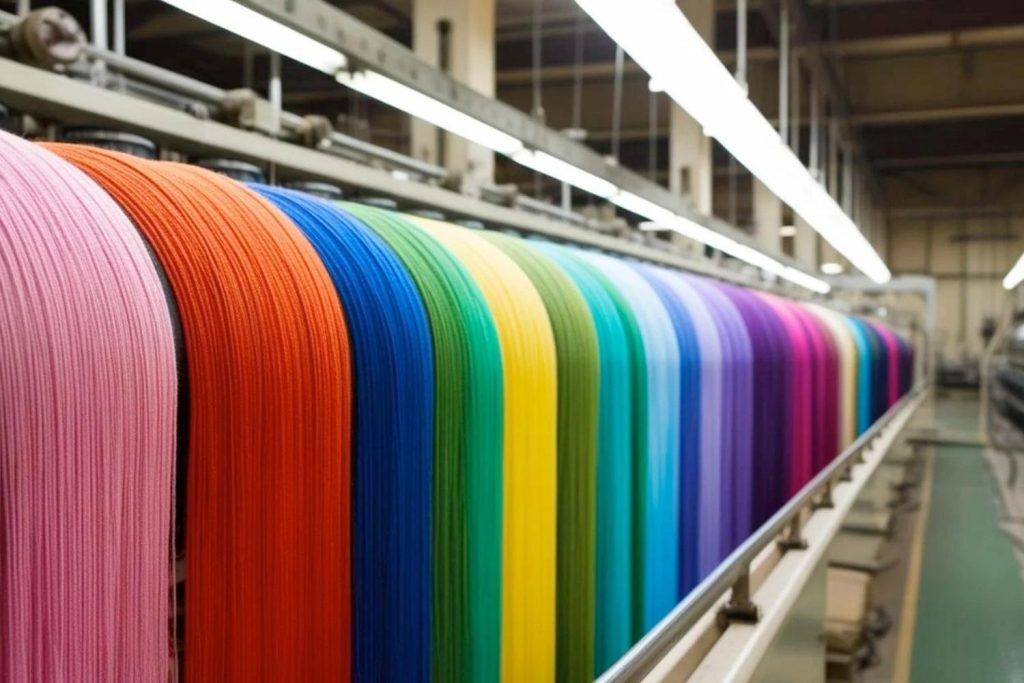
Energeia’s Solution: Comprehensive Pump Audit
To address these challenges, Energeia conducted a thorough pump audit across the company’s operations.
Pump Audit Implementation
The audit focused on various types of pumps within the facility, including:
- Hard Water Pumps
- Softener Pumps
- Generator Cooling Water Pumps
- Cooling Water Circulation Pumps
- Submersible Pumps
Key actions taken during the audit included:
- Monitoring Key Metrics: Power consumption, flow rates, discharge pressure, and head were monitored for each pump to establish a baseline for efficiency.
- Efficiency Assessment: Over 42 pumps were identified as running at 40% efficiency or less, highlighting the need for immediate action.
- Order and Implementation: The audit led to the customer placing an order for 52 new pumps, each properly sized and designed by Energeia to meet the specific needs of the operation.
- Documentation and Reporting: Energeia provided comprehensive documentation and reporting throughout the process.
- Monitoring and Verification: Post-installation, Energeia monitored and verified the savings achieved, establishing a new baseline for energy consumption and performance.