A Pharma R&D Facility’s Cooling Conundrum
For Mr. Suresh and his engineering team, managing the HVAC system at a leading pharma R&D facility in Hyderabad meant balancing precision and cost efficiency.
The labs were required to meet strict Good Manufacturing Practices (GMP) standards—precise temperature, air quality and humidity control – to protect critical research. Even minor deviations could jeopardize the sensitive medical research processes.
At the same time, the CEO demanded lower energy costs for the round-the-clock facility.
“We’re spending a fortune on utility bills, especially cooling. There must be a way to optimize this without disrupting operations.”
But the real struggle was in the day-to-day firefighting. Mr. Suresh and his team were stuck manually adjusting HVAC settings and responding to alarms, all while energy costs kept climbing. The toll was clear—on the equipment and on the people.
A full HVAC overhaul? Too risky and too expensive.
But staying on the same path? Financially and operationally unsustainable.
Was there a way to optimize their HVAC system, cut energy costs, and maintain strict lab conditions—without a massive upfront investment?
Key Stats
Monetary Savings Annually
Energy Savings Annually
CO₂ Emission Reduction
Customer Overview
A trusted R&D and manufacturing partner to the global life sciences industry.
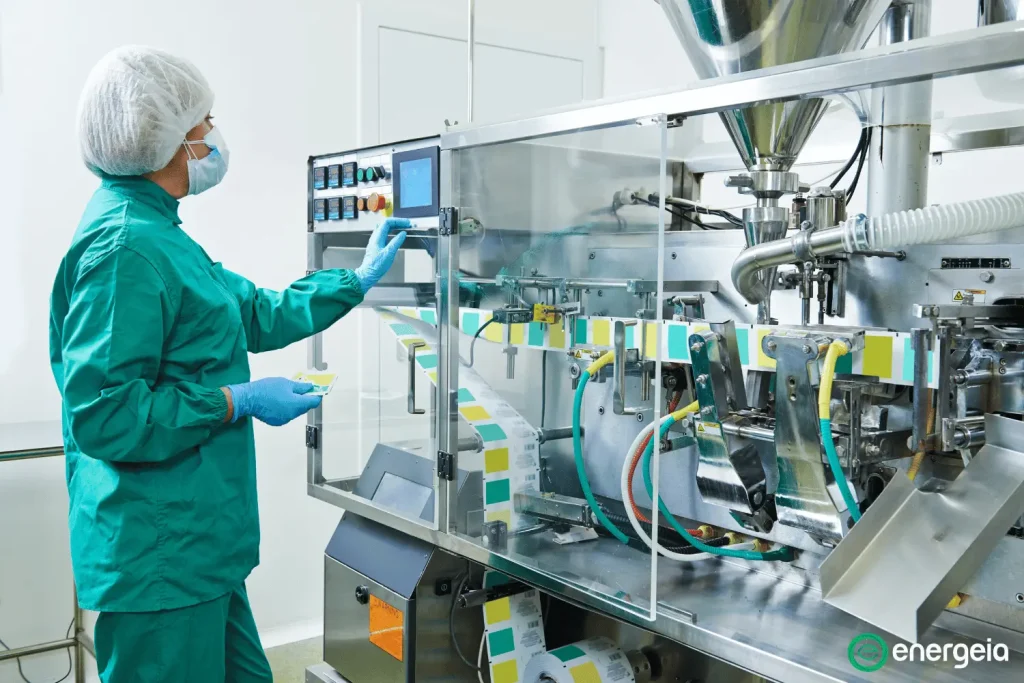
- Location: Hyderabad, India
- Facility: A leading pharmaceutical R&D and manufacturing company
- Existing Cooling System:
- Average chiller efficiency = 1.728 kW/TR
- Two 175 TR air-cooled chillers (one operational, one standby)
- Three constant-speed primary pumps
This state-of-the-art pharma facility operates 24/7, requiring strict environmental control to support sensitive research and manufacturing. However, an aging HVAC system was driving up energy costs and increasing maintenance efforts, putting pressure on both the operations and finance teams.
The Challenges
Precision, Efficiency, and Cost Control – A Tough Balancing Act
- High Energy Consumption – The system’s annual energy consumption for 2022-23 was 9,17,896 kWh, significantly increasing operational costs.
- Low-Efficiency Cooling Systems – The older chiller models were unable to match modern efficiency standards (they were averaging 1.728 kW/TR), leading to frequent maintenance issues and higher downtime risks.
- Lack of Real-Time Monitoring – Without continuous performance tracking, inefficiencies went unnoticed, making optimization difficult.
- Operational Constraints – Any solution had to be implemented without disrupting critical R&D and manufacturing operations.
- No Room for Large Capex – A full HVAC upgrade was financially unfeasible, so the team needed a cost-effective way to improve efficiency.
The Solution
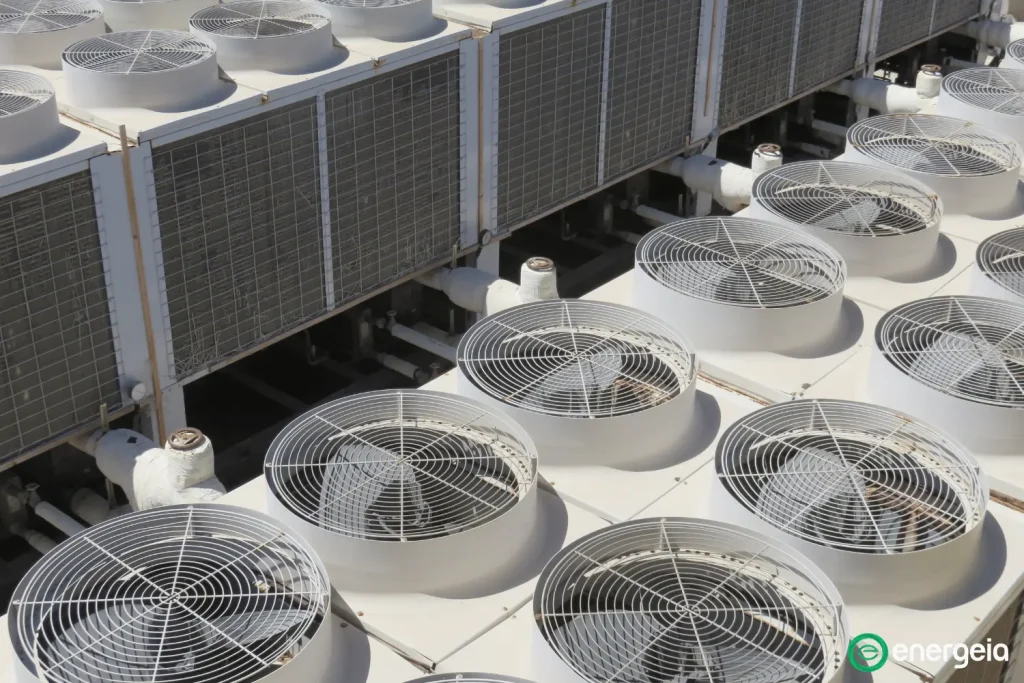
E-Chill: A Smarter Path to HVAC Efficiency without the Upfront Cost
To help the facility optimize its HVAC system without disrupting operations or requiring major capital investment, Energeia followed a structured approach:
- Comprehensive Energy Audit – We conducted a real-time IoT-based HVAC energy audit using our Energy Monitoring System (EMS) to analyze cooling demand, energy losses, and efficiency gaps.
- Identifying Optimization Opportunities – Our BEE-certified energy managers reviewed the data to pinpoint inefficiencies in chiller operations and uncover potential savings.
- Zero CAPEX Proposal – Based on the findings, we designed a cost-effective solution to enhance efficiency without requiring any upfront investment from the company.
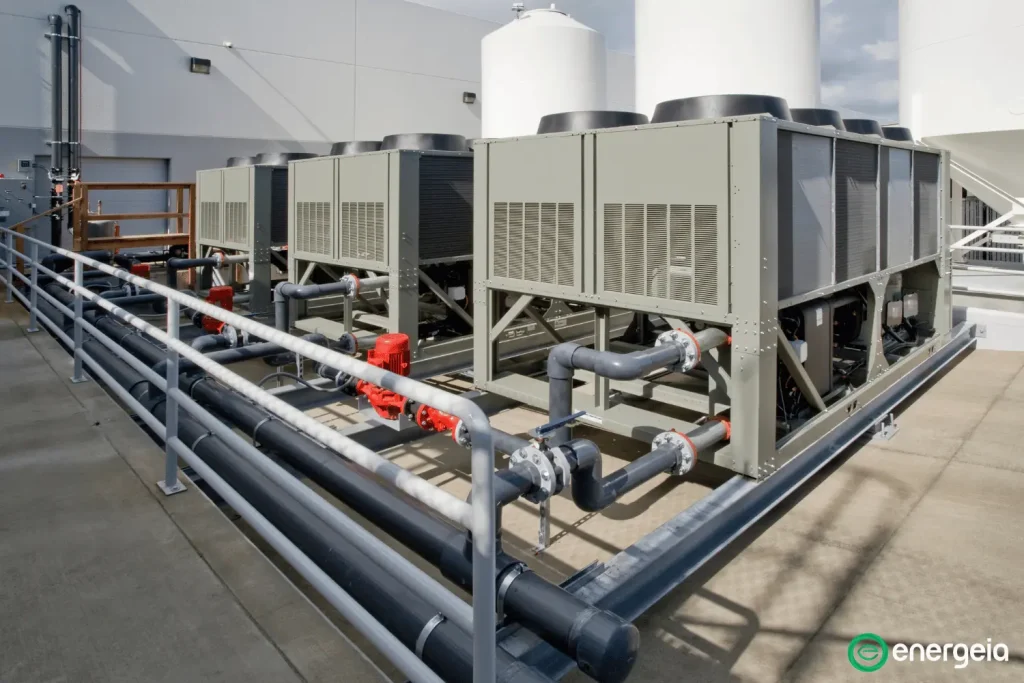
Upgrading Cooling, Maximizing Savings – With Zero Disruptions
To drive energy efficiency and cost savings, Energeia implemented the following measures:
- Chiller Replacement – One of the aging 175 TR chillers was replaced with a new energy-efficient model, achieving a projected efficiency of 0.95 kW/TR.
- Performance Assurance – The newly installed air-cooled chiller was guaranteed to maintain an efficiency of 1 kW/TR, ensuring long-term energy savings.
- IoT-Enabled Monitoring – We integrated IoT-based energy monitoring, allowing for continuous tracking of chiller performance and real-time measurement of energy savings.
The E-Chill ESCO Shared Savings Model
A Win-Win Financing Model
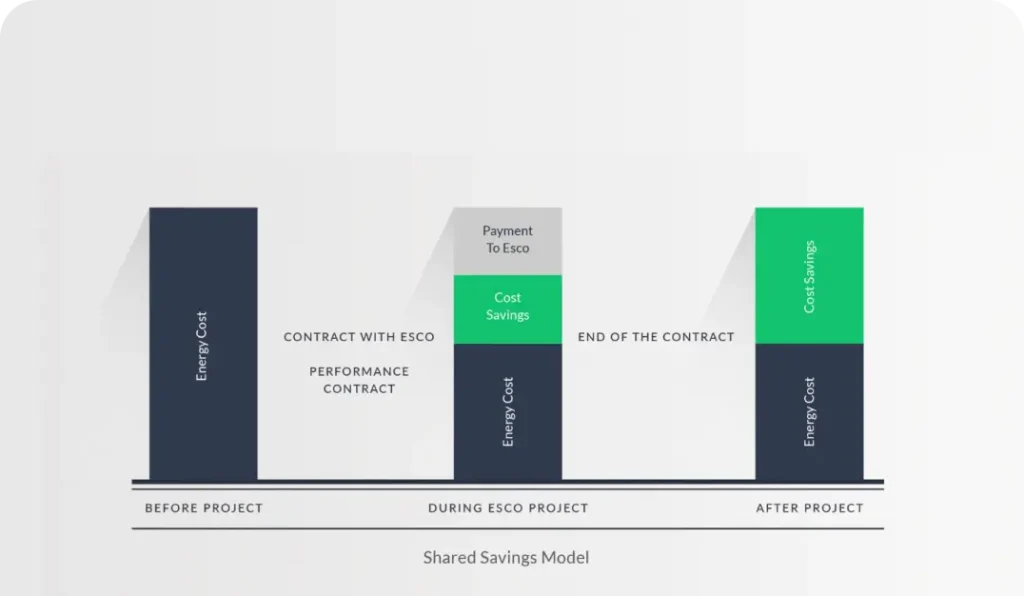
To eliminate financial barriers and ensure seamless execution, Energeia implemented the chiller replacement under a Shared Savings ESCO model, handling every aspect of the project, including:
- Zero Capex for the Customer – The facility received a fully upgraded, energy-efficient chiller at no upfront cost.
- No Maintenance Expenses – For eight years, all maintenance and servicing costs are fully covered by Energeia, ensuring reliable operation without additional financial burden.
This solution delivered guaranteed efficiency improvements while eliminating the risk of capital expenditure, making it a win-win for the company’s engineering and finance teams.
To learn more about Energy Services Companies, click here.
Ready to optimize your facility’s HVAC system?
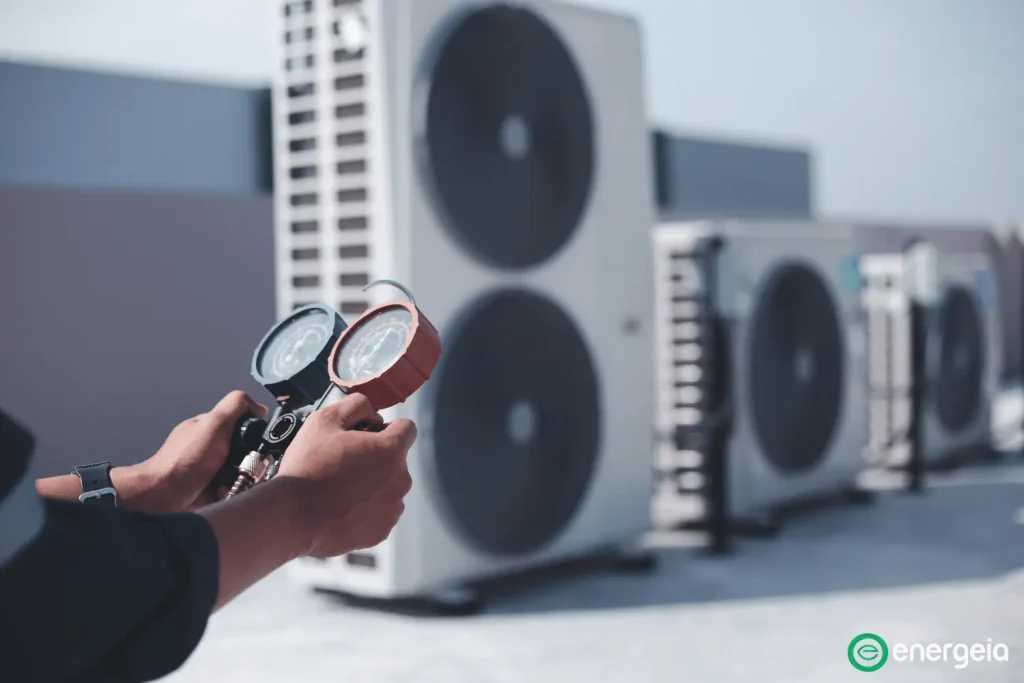
📞 Book a Free Energy Appraisal Today: +91 9319271849
✉️ Email: sales@energeia.in