Executive Summary
A global automotive component manufacturer struggled with inefficient compressed air systems in their Jaipur facility. Energeia’s comprehensive compressed air audit revealed substantial energy-saving opportunities. Our recommendations, including compressor replacements, centralized control systems and operational optimizations, delivered annual savings of 2,75,391 kWh, translating to ₹22 lakh in cost savings.
Key Stats
Monetary Savings Annually
Energy Savings Annually
CO₂ Emission Reduction
Customer Overview
The client is a leading provider of technology and services in India, with a strong presence in Mobility Solutions, Industrial Technology, Consumer Goods, and Energy & Building Technology. The Jaipur factory is one of the company’s many manufacturing sites in India. This plant plays a crucial role in its automotive component manufacturing operations.
The Challenges
- Energy Inefficiency: The compressed air system was operating at a higher specific power consumption (0.255 kW/CFM) compared to the industry standard (0.180 kW/CFM).
- Mismatched Capacity: The existing compressor setup was not optimized for varying demand, especially during night shifts.
- Operational Inefficiencies: Multiple compressors were often running simultaneously, leading to energy wastage.
- Lack of Centralized Control: Absence of a centralized system resulted in suboptimal compressor sequencing and operation.
- High Energy Costs: The plant was spending approximately ₹63 lakh annually on energy for the compressed air system.
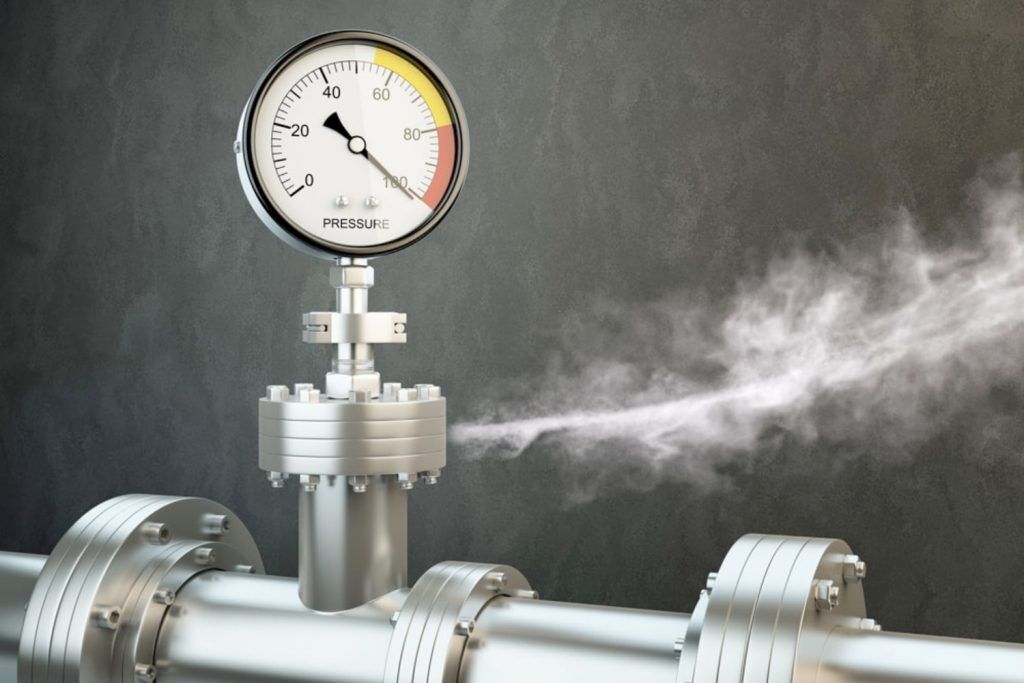
Energeia’s Solution: E-Air Optimization
Energeia conducted a detailed audit of the compressed air system and proposed a comprehensive optimization strategy:
- Compressor Replacement:
- Smaller VFD-driven compressor for night shifts
- An Energy-efficient compressor for day shifts with higher FAD, eliminating the need to run two air compressors
- Centralized Control System implementation for optimized compressor sequencing during different demand requirements
- Additional Recommendations:
- Buffer air receiver installation
- Level-based auto drain system
- Energy-efficient air guns
- Aluminum piping consideration