A Costly Pumping Problem
At a leading glass manufacturing plant in Haryana, Mr. Sharma and his operations team were facing a hidden energy drain.
The factory ran at full capacity, producing glass for automotive and construction industries. But beyond the tempered glass exterior, the operations team was struggling with excessive energy consumption of its inefficient water pumping system.
“The pumps weren’t delivering the pressure needed for production but their power use was very high,” says Mr. Sharma.
“With repeated repairs and high energy costs, we wanted to see if replacing them with energy efficient pumps was worth it, but were struggling to understand where to begin.”
Energeia stepped in as a trusted, unbiased partner, conducting a comprehensive Pump Audit to uncover the exact inefficiencies in the water pumping system and suggest high-ROI energy-saving solutions.
Key Stats
Monetary Savings Annually
Energy Savings Annually
CO₂ Emission Reduction
Customer Overview
An NSE-listed Glass Manufacturer in Haryana
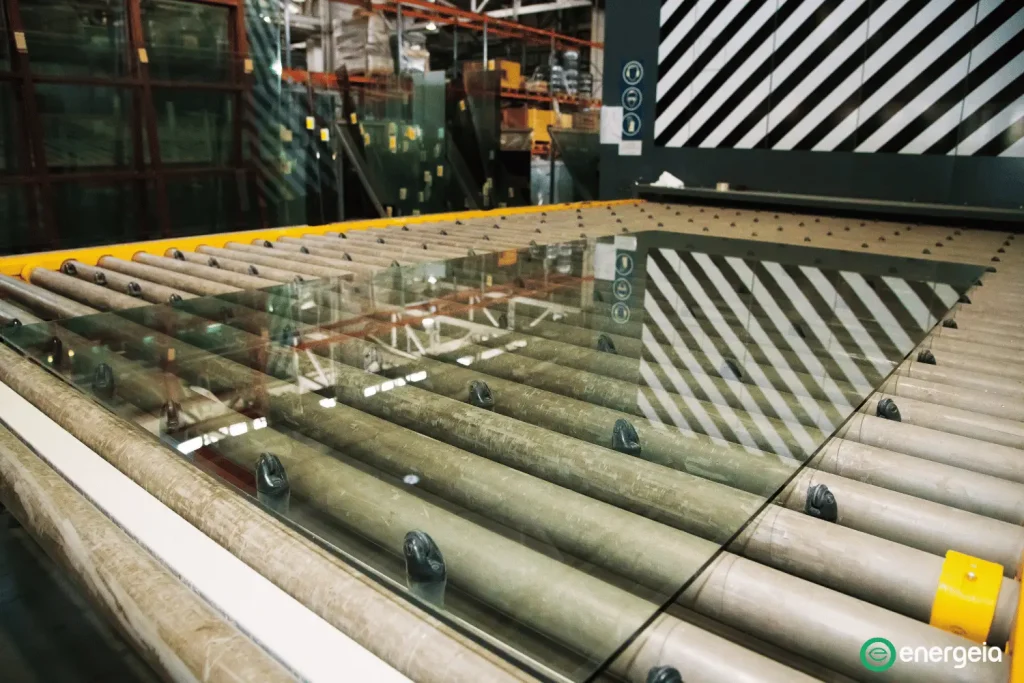
The company is one of India’s leading manufacturers of integrated glass solutions, catering to the automotive, building & construction, and consumer segments. The company operates state-of-the-art manufacturing facilities across India. The production facility in Bawal, Haryana was their flagship factory, where a large amount of energy is currently consumed by grinding pump systems.
- Location: Bawal, Haryana, India
- Facility: Factory built in 1987 to produce toughened glass products for automotive windshields
- Existing Pumping System: 10 water circulation pumps
The Challenge
Frequent, inefficient and costly repairs
This glass manufacturing plant’s water pumping system had been working tirelessly for decades—but time was catching up.
- Frequent Repairs: Built in 1987, the plant still relied on antiquated water pumping technology that broke down often, interfering with smooth operations.
- Low Efficiency: Mr. Sharma’s team suspected some pumps were running at less than 20% efficiency, but needed a clear operational diagnosis.
- Sky-High Energy Bills: With pressure from the finance team to cut energy costs, they needed a solution that reduced their energy costs while improving reliability.
The Solution
Energeia’s Comprehensive Pump Audit
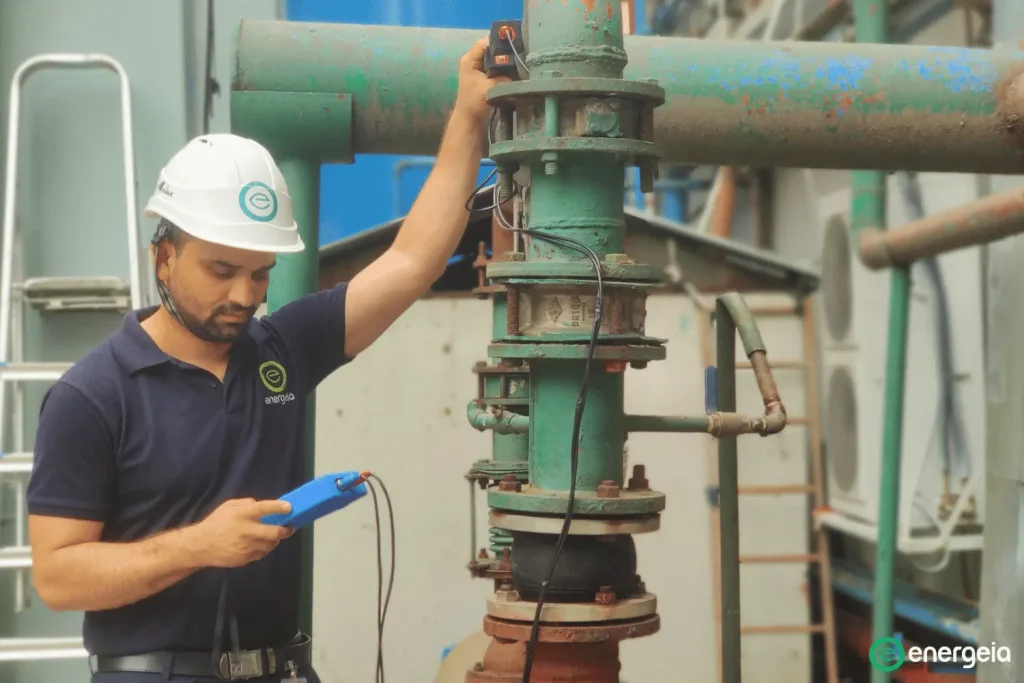
Mr. Sharma’s team needed clear, data-backed insights to fix their pump inefficiencies. Energeia’s BEE-certified energy auditors conducted a comprehensive pump system audit, covering 10 water circulation pumps across key production areas.
- On-Site Inspection: Our engineers visited the Bawal plant, assessed the pumping equipment, and interviewed staff to identify the key operational issues.
- IoT Monitoring: We installed real-time energy meters to track power usage patterns throughout the day, pinpoint the exact pressure & flow drops, and baseline each pump’s actual efficiency.
- Data-Driven Analysis: Using the data collected over 15 days, Energeia’s in-house energy analysts modeled the impact of potential energy-saving measures.
- Actionable Audit Report: We presented our findings with prioritized recommendations and ROI calculations to Mr. Sharma’s team.
Key Findings
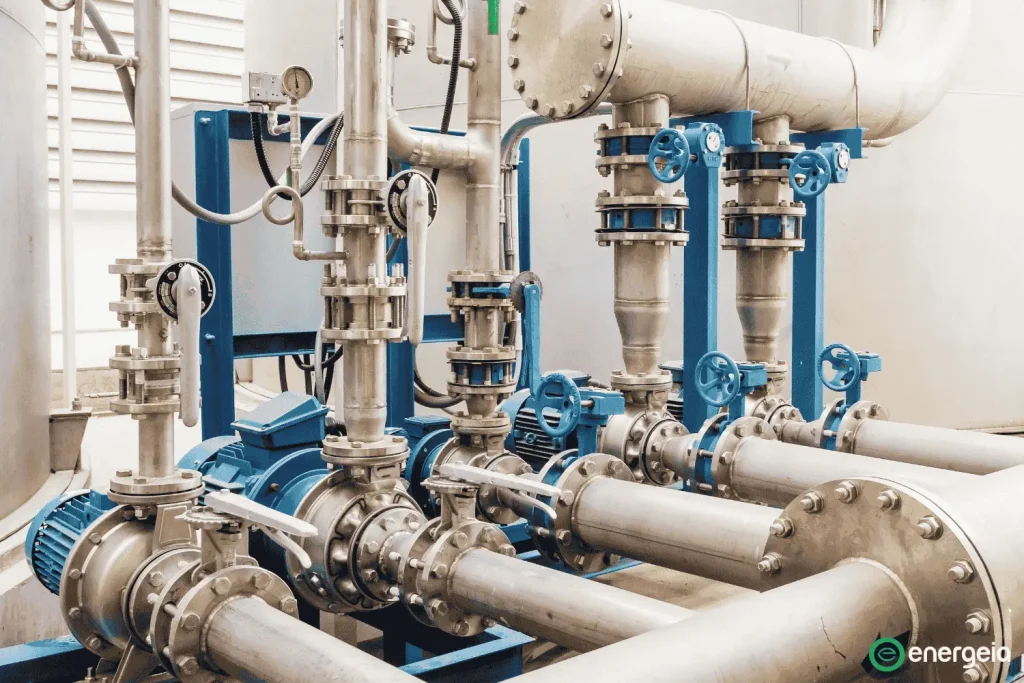
Energeia’s audit uncovered two major inefficiencies draining energy and increasing costs:
- Aging and Inefficient Pumps: Many pumps were too old to cater to the actual demand, leading to low efficiency and wasted energy.
- Frequent Maintenance Issues: Constant repairs weren’t just adding to the hidden operational costs, but also disrupting operations and reducing system reliability over time.
Should You Replace or Optimize Your Pumps?
For this factory, replacing 6 very old, highly inefficient pumps with energy-efficient IE-3 motor models was the most cost-effective solution. It would save Mr. Sharma’s team ₹17.38 lakh annually in power costs.
Metric | Before (Old System) | After (New System) | Improvement |
---|---|---|---|
Annual Energy Use | 2,88,000 kWh | 1,98,000 kWh | 🔽 31% Reduction |
Annual Power Cost Savings | – | ₹17.38 Lakhs | 💰₹17.38 Lakh Saved |
Average Pump Efficiency | 40% | 70% | ✅ 30% Increased Efficiency |
Additionally, we suggested 3 more targeted improvements in the water pumping system for the rest of the pumps:
- Pressure control adjustments to improve production reliability
- Right-sizing pumps to the plant’s actual demand patterns to cut energy waste
- IoT energy monitoring to track the pumps’ performance in real-time and tweak operations as needed
Beyond Just Cost Savings
A More Reliable, Efficient Operation
With Energeia’s audit report in hand, Mr. Sharma’s team could now confidently present a data-backed case for upgrading their water pumping system to senior management.
“Before, we knew we had a problem but didn’t have the numbers to prove it,” says Mr. Sharma. “Now, we have a clear roadmap to reduce our pumping power costs and make our production process more stable.”
By investing in smart pump optimization, the factory not only saved energy but also improved operational reliability for years to come.
📞 Book a Free Energy Appraisal Today:+91 9319271849
✉️ Email: sales@energeia.in