Executive Summary
A large manufacturing company in Faridabad, spending ₹15 crore annually on energy bills, faced challenges in managing their energy use. Energeia’s Energy Monitoring System (EMS) led to ₹17.5 lakh in savings, 188 tonnes of CO₂ reduction, and higher machine uptime.
Key Stats
Monetary Savings Annually
Energy Savings Annually
CO₂ Emission Reduction
Customer Overview
Established in 1982, a prominent manufacturing company specializes in producing Grey Iron, Ductile Iron, and SiMO machined castings, crucial for the automobile and other industries. With a connected load of 4 MW, the company incurs annual energy costs between Rs. 14.4 – 18 crore.
The Challenges
Operating in an energy-intensive industry, the company faced significant challenges in managing its energy consumption. The key issues included:
- Inability to meet Specific Energy Consumption targets per tonne of metal produced.
- Lack of remote monitoring, leading to accountability issues among production workers.
- Difficulty in tracking daily energy consumption variations.
- Reliance on manual metering, prone to human errors.
- Absence of a system to monitor the time cycle of each batch of heat.
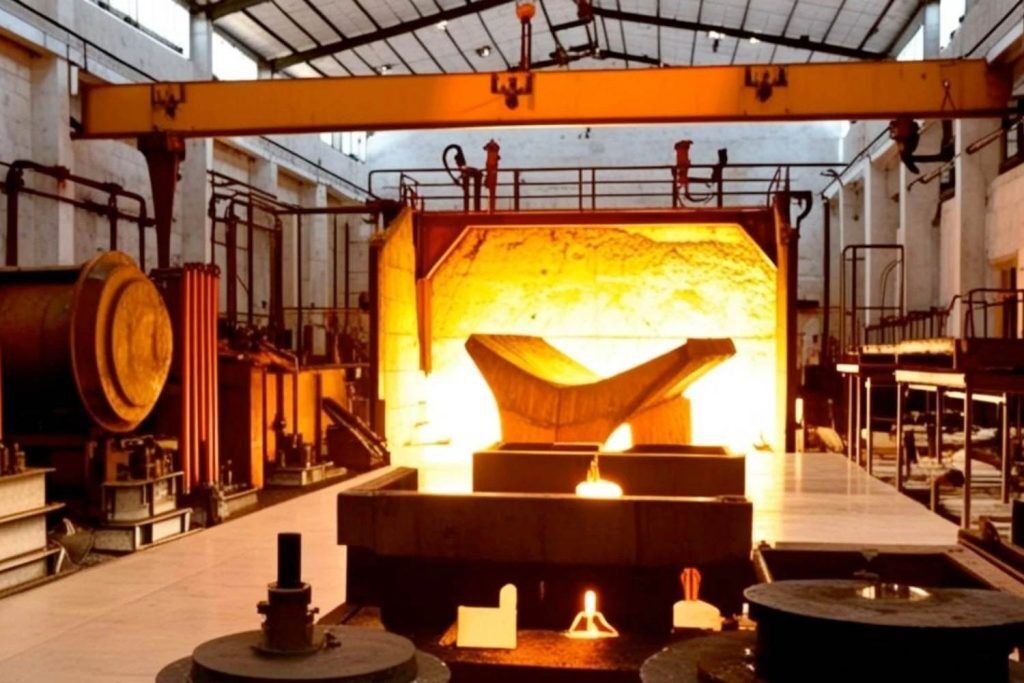
Energeia’s Solution:
Energeia implemented a comprehensive Energy Monitoring System (EMS) at the facility. The key components of this solution included:
Energy Monitoring System (EMS)
- Installation of Energy Sensors: Various energy sensors were installed to provide continuous data streaming to Energeia’s servers.
- Dedicated Dashboard: A dedicated dashboard was developed for the maintenance team to monitor energy usage in real-time and identify areas of high or unusual consumption.
Financing Model
The project was executed under a subscription business model, featuring:
- Complete financing of the hardware infrastructure by Energeia.
- Shared savings from retrofit solutions between Energeia and the company.
- A monthly Software as a Service (SaaS) fee paid by the company for data point monitoring on the EMS.