Digitization of energy data in industries has transformed how they consume and monitor energy. The transition from manual energy data logging to real-time energy monitoring systems is transforming industries. This change unlocks value in energy efficiency. It also serves as the backbone of corporate sustainability and ESG metrics.
Bad Information begets Bad Metrics
Metrics are an abstraction of their underlying data or more simply put, bad information begets bad metrics. If data collection and processing practices are inaccurate, the metrics and insights derived will amplify the inaccuracy. In industrial settings, operators often manually log data into logbooks, which is later entered into Excel sheets. This process introduces multiple points of human error. Statistically, professional operators face a 4% error rate in data entry. For untrained operators using two-stage manual entry, the error rate is significantly higher. Additionally, data logging frequency is limited to 2-4 times daily per sensor. This frequency, usually at shift start and end, results in low-resolution energy data. Consequently, the insights and actions that can be taken are severely limited.
An Energy Monitoring System (EMS) collects energy data from connected meters and instruments with high accuracy. It can record data at a frequency as high as every second. Even though in most cases 5-10 minute data logging frequency is sufficient for most energy efficiency and predictive maintenance projects. EMS system analyses, conducted monthly or quarterly, provide insights into energy data in industries. Organizations use these insights to support ESG and sustainability metric calculations. An EMS with an in-built Monitoring and Verification (M&V) capacity informs ESG metrics like GRI 302. It also tracks improvement projects under ISO50001.
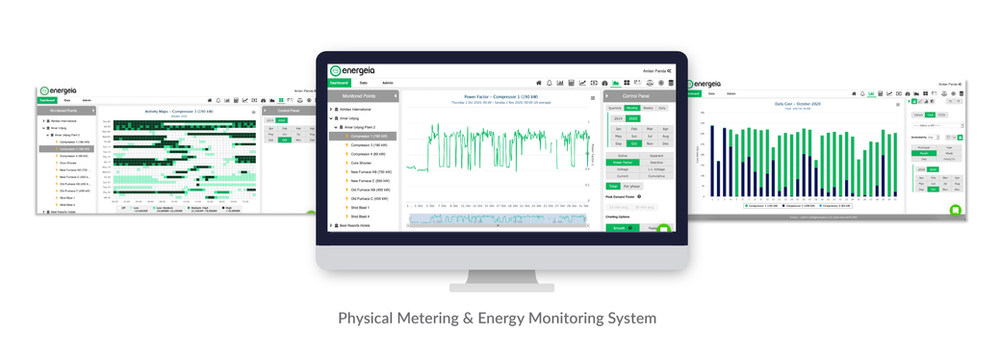
The Cost of Ignoring Energy Data in Industries
“The price of light is less than the cost of darkness.”
Arthur C. Nielsen
“The lack of awareness stems from wilful or unwitting ignorance of energy consumption across industrial processes”, said. Dr. Arunabha Ghosh from CEEW in an article for the Financial Express. He also highlighted that ” Enterprises tend to only look at monthly energy bills and overall energy consumption without correlating the data with specific equipment efficiency or energy intensity of output. They often have no monitoring tools or energy-efficiency practices, nor any data on performance benchmarks of EETs used for different industrial processes in each sector.”
This ignorance is short-sighted for two reasons. First, compliance in industrial emissions and energy is becoming increasingly data-driven. It is not a question of if EMS will become a necessity but when. The Central Pollution Control Board (CPCB) mandates automatic reporting systems to track boiler stack emissions and effluent treatment plants (ETPs). Facilities already pay electricity and diesel bills, which ensure data collection. Second, not having deep insights into energy costs, which represent 30-45% of operating costs, is a missed opportunity. These insights hold significant potential for cost-saving and sustainability enhancements. The price of light is not as high as it seems. Moreover, according to Hemant Mallya from CEEW, “Precisely measuring energy consumption increases the odds of investment in EETs (Energy Efficient Technologies) nearly six-fold.” This cost of darkness may be hard to recognize in the short term. However, it will undoubtedly become a competitive disadvantage in the long term.
SEBI: ESG Reporting Norms and Mandate
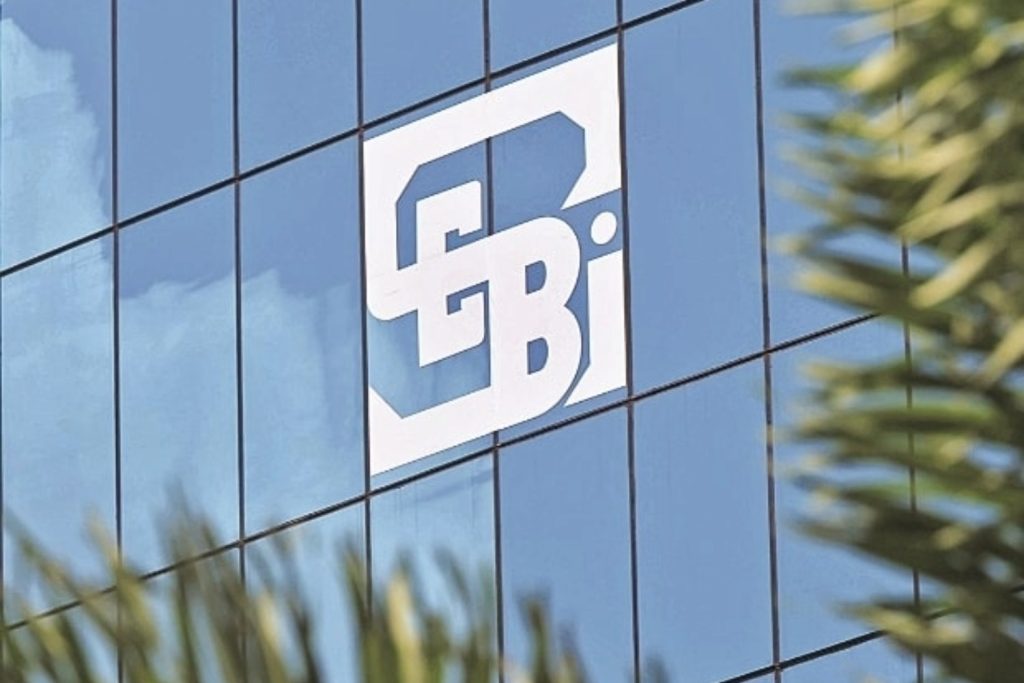
On the 10th of May 2021, the Securities and Exchange Board of India (SEBI) issued a circular on new sustainability disclosure norms. The top 1,000 listed companies by market capitalization must implement these norms by FY23. These disclosures could be made using the following reporting standards GRI, SASB, TCFD, or Integrated Reporting. While these disclosures are voluntary for 1,000 listed companies for FY 2021-22, they will become mandatory from FY 2022-23.
As the top 1,000 listed companies prepare for ESG disclosures, they must establish a comprehensive data collection and processing system. This system is essential before the disclosures become mandatory. Implementing a facility-wide Energy Monitoring System (EMS) is a key step in this process. An EMS can unlock energy efficiency and provide data for ESG metrics like GRI 302. The utility of energy data in industries has expanded far beyond accounting for operating expenses. It now serves as the foundation for monitoring sustainability projects. It also influences the interest rates at which companies can raise debt for green capital investments. Furthermore, it helps improve ESG metrics, ultimately bolstering the company’s share price.