

Overview
A Tier-1 Indian Automobile Component Manufacturer, with over 650 employees and an annual revenue exceeding $130 million, has been investing in a program to improve energy efficiency in their factories, specifically focusing on their air compressors.
Energeia began by conducting a comprehensive Compressed Air Audit for their facility in Haryana. The audit identified areas for improvement, addressing issues that contributed to increased energy consumption by compressors (measured in kWh) and enhancing the specific power of the compressed air system (measured in kW/cfm). We also helped source, finance and deploy low-cost, high-yield solutions to optimise this facility’s air compressor usage.
The facility had 4 air compressors with a total installed capacity of 1700 cfm. On average, the air compressor plant consumed 2500-2800 kWh per day, resulting in an annual air compressor cost of ₹75 Lakhs — this was before they partnered with Energeia.
Key Stats
Annual KWh Reduction = 1.64 lakh kWh (₹)
Annual Cost Savings = ₹13.12 Lakhs
Annual CO₂ Emission Reduction = 1.35 Lakh Tons
Challenges
Identifying the Challenges

Energeia, an energy efficiency company, came on board in 2021 to conduct an onsite Investment Grade Audit (IGA) and identify savings opportunities. Energeia has a proven track record globally, reducing energy consumption and costs for large industrial companies.
We do this by combining cutting-edge engineering, financing, and technology solutions that aim to create long-term, planet-positive solutions and unlock profitability through sustainability.
An initial period of system assessment and base-lining followed, where the Energeia team worked very closely with the client to coordinate and collaborate on the best possible energy efficiency improvements given the available budget and targets. Project implementation commenced on November 2021 with testing and snagging continuing into 2022.
The IGA was key to identify potential opportunities and savings. It was important to not only understand the equipment on site, but how it was being operated. By collecting historical data as well as going to site and doing in-depth testing and measurement, as well as interacting with the air compressor operators and maintainers, Energeia was able to identify various operational challenges and ways to optimize the overall system operation.
Challenges Found
When starting this process, it was immediately clear that very little to no data was being collected from the factory’s air compressors. The usage data was essentially a black box.
After Energeia installed its E-Air IoT-based monitoring system, which consisted of energy meters, pressure sensors, flow meters, and a data acquisition system, compressed air data was collected at a 1-second interval for a period of 30 days.
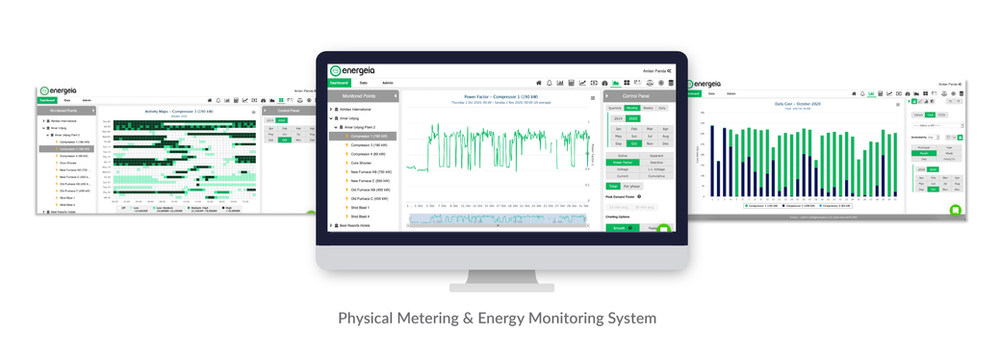
Energeia’s BEE-certified analysts used this data to identify 4 key challenges related to the facility’s air compressors –
- Ineffective Compressor Room Layout
- Undersized Compressed AirNet
- Pipeline Design Issues
- Improper Receiver Design Sizen
Moreover, once the air compressor data was visualized in Energeia’ IoT platform, we found that the facility was also facing an alarming pressure drop in one of the critical production areas which needed further investigation.
Solutions
Energeia signed a Shared Savings ESCO contract with the customer for 5 years.
After rigorous analysis, Energeia implemented the following solutions to optimize air compressor usage—
- Deployed a pressure-based control system which enabled the correct combination of Air Compressors to run, depending on the plant demand.
- Increased the internal pipeline size, thereby reducing the alarming pressure drop.
- Changed the layout of the Compressor Room to maximize efficiency.
- Reconfigured all compressor set-points so the systems could cater dynamically to varying plant demand in a more efficient manner.

Additional Benefits
- The real-time monitoring and visualization of factory’s energy consumption helped the management, specially the Plant Head and CEO proactively deal with any safety alerts or potential downtime.
- The number of breakdowns reduced as preventive maintenance became easier.
- All the maintenance staff and engineers were upskilled by the Energeia team and taught the best practices to optimize production throughput.
Looking to elevate your plant’s air compressor energy efficiency too? Click the button below!